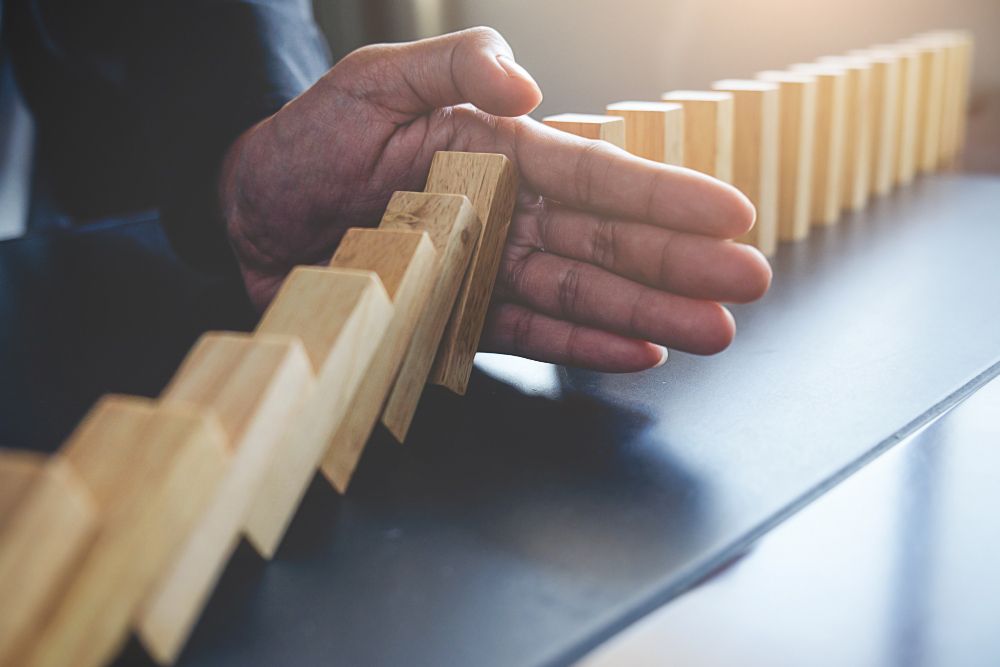
ProBDE MES wspiera firmy w czasie zawirowań rynkowych
Firmy produkcyjne, które wdrożyły oprogramowanie klasy MES (Manufacturing Execution System), odnotowują spektakularne rezultaty we wszystkich obszarach związanych z wytwarzaniem swoich produktów. Czy zatem MES jest optymalną odpowiedzią na wyzwania rynkowe i organizacyjne, jakie pojawiły się wraz ze spowolnieniem wywołanym pandemią COVID-19?
O metodach optymalizacji produkcji napisano już niezliczoną ilość opracowań. Praktycy zajmujący się zawodowo tym tematem mogą oczywiście się spierać, czy najwłaściwszą drogą do poprawy wskaźników jest wyjście od konsultingu i analiz procesów, czy może lepiej najpierw wdrożyć dedykowane oprogramowanie, takie jak MES, by dopiero potem wprowadzać pożądane zmiany. Rozwiązania MES, które w założeniu mają wspierać zarządzanie produkcją, w sposób ciągły monitorują procesy wytwarzania, wizualizują je w czasie rzeczywistym oraz dostarczają rzetelnych, twardych danych. Dzięki informacjom i raportom dostępnym bezpośrednio w MES kierownictwo zyskuje wiele możliwości ciągłego doskonalenia swojego biznesu. W efekcie pracownicy obszaru produkcji działają efektywniej, maszyny mają mniej przestojów, zwiększają swoją wydajność i dostępność, co przyczynia się do poprawy samej jakości. Zarazem zmniejsza się ilość strat materiałowych.
Warto podkreślić, że niezależnie od przyjmowanych metod usprawniania produkcji, gra toczy się zawsze o to samo – o miarodajne MONITOROWANIE PROCESÓW oraz o wynikające z niego INFORMACJE. Kto ma dostęp do kluczowych danych z obszaru wytwarzania, ten ma możliwość wprowadzenia niezbędnych usprawnień. A za tym idzie poprawa wskaźników, takich jak większa zyskowność czy skrócenie czasów realizacji zamówień, a także ogólnie silniejsza pozycja konkurencyjna.
Korzyści z użytkowania MES od lat są znane, natomiast nieco nowe światło rzucił na nie wybuch pandemii COVID-19, który wywołał poważne zawirowania rynkowe, wskutek czego zaburzeniu uległa strona popytowa. Z jednej strony w wybranych branżach nagłe doszło do załamania lub dużego ograniczenia konsumpcji, z drugiej strony na niektóre rodzaje wyrobów pojawił się niespodziewany, niespotykany dotąd wzrost zapotrzebowania. Obok tych komplikacji pojawiły się koszty. Jak przyznają firmy produkcyjne, poważną trudność spowodowały wymogi i obostrzenia sanitarne związane z sytuacją epidemiczną i lockdown-em. W zakładach należało szybko wdrożyć szereg procedur bezpieczeństwa. Miały one chronić nie tylko zatrudnionych, ale również same firmy przed groźbą zamknięcia w przypadku wykrycia u któregoś z pracowników zakażenia wirusem. W opinii przedsiębiorstw to właśnie zamknięcie zakładu jest obecnie największym ryzykiem. Aby je ograniczyć do minimum, przedsiębiorstwa zmuszone były ponieść wysokie i nieplanowane koszty.
W trudnej sytuacji rynkowej firmom łatwiej przetrwać, gdy do dyspozycji są pewne rezerwy. Jednak, gdy ich brakuje, w przetrwaniu biznesu pomaga przede wszystkim wiedza – o tym, jak działa firma, czym dokładnie dysponuje, jakie ma bieżące ograniczenia oraz możliwości. Trudno sobie wyobrazić, by tego rodzaju informacje były przetwarzane w przedsiębiorstwach bez rozwiązań informatycznych. W przypadku firm produkcyjnych, które nagle stają wobec trudnej sytuacji rynkowej, ratunkiem może być właśnie rozwiązanie MES.
20% skok efektywności dzięki MES
Mieć dane, to móc działać efektywniej. Aby zatem lepiej zrozumieć, jak ważną rolę odgrywa MES w organizacji zajmującej się produkcją, warto sięgnąć po prawdziwe przykłady. PipeLife Polska S.A. jest częścią firmy Wienerberger, międzynarodowego koncernu z branży budowlanej. Spółka obecnie realizuje produkcję na zamówienie z wielu krajów Unii Europejskiej. W całym holdingu to właśnie w Polsce pracuje największa wtryskownia, której wolumen produkcji obejmuje aż kilka tysięcy wyrobów. Każdego miesiąca spółka wytwarza wiele ton wyrobów (kształtek) o bardzo zróżnicowanej masie – od kilku gram do 30 kg. Zarządzający przyznają dziś, że przy takiej skali działania MES jest jednym z fundamentów, bez którego nie byłoby możliwe efektywne działanie całego ekosystemu produkcji. Jednak firma nie korzystała przecież z MES od początku swojej działalności. Zanim wdrożono takie rozwiązanie, dane z obszaru harmonogramowania i monitorowania produkcji były przetwarzane w arkuszach kalkulacyjnych. Arkusze nie były integrowane z systemem ERP, co powodowało, że zarówno zarządzanie jak i poszczególne procesy produkcji były mało wydajne. Konsekwencjami „ręcznego” przetwarzania danych były błędy, zbyt duża czasochłonność ich wprowadzania, a także spore ograniczenia w generowaniu użytecznych i wiarygodnych raportów. W PipeLife wdrożono system ProSeS BDE. Co się zmieniło po jego uruchomieniu? „Nasza efektywność skoczyła o 20%, jeszcze zanim podjęliśmy jakiekolwiek działania optymalizujące proces. Proszę sobie wyobrazić, co to znaczy przy tak dużej skali działalności. System pokazał nam, jak wielkimi wolnymi mocami wytwórczymi dysponowaliśmy” – wspomina Janusz Manteufel, Zastępca dyr. Technicznego w PipeLife Polska S.A.
Gdy w obszarze produkcji praca odbywa się w oparciu o arkusze kalkulacyjne, sprawą kluczową staje się skuteczny monitoring i nadzór nad danymi. To generuje spore koszty, angażuje znaczne nakłady pracy, a przy pewnej skali działania staje się uciążliwe i w dodatku wcale nie gwarantuje, że końcowe informacje są rzetelne. W wyniku wdrożenia ProSeS BDE w PipeLife większość tych problemów udało się wyeliminować lub zminimalizować, ponieważ system w sposób automatyczny rejestruje dane bezpośrednio z każdego urządzenia w parku maszynowym. Dzięki wcześniejszemu opomiarowaniu maszyn, można analizować szczegółowe dane tak w trybie on-line – „tu i teraz”, jak i w ujęciu historycznym. „Największą wartością systemu MES jest to, że dysponujemy wiarygodnymi danymi. Nikt z użytkowników, czy to operatorów maszyn, czy liderów zespołów, nie może ich reinterpretować na swoją korzyść, ponieważ czarno na białym widać wszystko – jak długo pracowały maszyny, ile miały przestojów, jak dużo wyprodukowały elementów, ile sztuk było wybrakowanych, czy jak długie są same cykle produkcyjne. Łatwy dostęp do tych wszystkich danych powoduje, że decydenci na różnych poziomach struktury organizacyjnej mogą bardzo szybko uzyskać dowolne raporty i zestawienia. Są one pomocne nie tylko w produkcji, ale również w sprzedaży, logistyce czy dziale zamówień” – dodaje Janusz Manteufel. Podkreśla przy tym również, jak wiele działań udaje się usprawniać dzięki MES. Wskazuje m.in.: skracanie cyklów produkcyjnych poszczególnych wyrobów (czas liczony w sekundach), skracanie czasu przezbrojeń, efektywniejsze prace w dziale Utrzymania Ruchu (prace konserwatorskie, remonty), zautomatyzowane planowanie i harmonogramowanie produkcji na podstawie danych spływających z zamówień, z uwzględnieniem bieżącej dostępności maszyn i wszystkich planowanych przestojów. System pomaga też w identyfikowaniu wąskich gardeł oraz punktów do optymalizacji. Pomaga również lepiej alokować zasoby osobowe do poszczególnych typów przezbrojeń. Z kolei dzięki integracji MES z systemem ERP SAP korzyści odnoszą pracownicy spoza obszaru produkcji – m.in. z działów sprzedaży, controllingu, finansów i logistyki.
MES wspiera system premiowy i redukuje czas przestojów
Innym przykładem przedsiębiorstwa, które odnosi korzyści po wdrożeniu rozwiązania klasy MES, jest firma Dr. Schneider Automotive Polska, specjalizująca się w produkcji podzespołów w branży motoryzacyjnej, elementów wykończenia pojazdów i rozwiązań dla systemów klimatyzacji. Firma dostarcza podzespoły dla większości znanych marek samochodów. System ProSeS BDE pomaga w ustaleniu wysokości premii dla niektórych grup pracowników okołoprodukcyjnych. W weryfikacji wyników pracy są pomocne obliczenia realizowane w MES. Taki model wspiera pracę na wspólny cel, jak i pracę zespołową. „Największa zmiana odczuwalna po wdrożeniu ProSeS BDE polegała na podniesieniu wiarygodności danych z produkcji. Dane są rzetelne, ponieważ pobierane są automatycznie bezpośrednio z maszyn. Inna ważna korzyść wiąże się z wizualizacją tego, co dzieje się w halach produkcyjnych. Dzięki systemowi nie tylko widzimy w czasie rzeczywistym, jak pracują maszyny, ale również to, czy pracują one zgodnie z dziennym harmonogramem. W wyniku wdrożenia udało nam się zoptymalizować proces usuwania awarii i nieprzewidywalnych przestojów. Przed wdrożeniem MES operator musiał dzwonić do ustawiacza, po czym dopiero uruchamiany był proces naprawy. Mieliśmy długie czasy przestoju. Dziś, gdy tylko pojawi się problem z maszyną, ustawiacz natychmiast to widzi i podchodzi do maszyny od razu. Dzięki ProSeS BDE udało nam się znacznie skrócić czas usuwania awarii” – mówi Michał Pikus, Zastępca Dyrektora Zakładu, Kierownik ds. Łańcucha Dostaw w Dr. Schneider.
W firmie każdego dnia odbywają się spotkania, podczas których analizowana jest praca maszyn i awarie zarejestrowane w ciągu ostatnich 24 godzin. Zespoły w oparciu o twarde dane definiują działania zaradcze i decydują, jak zachować się w obliczu zdiagnozowanych problemów i sytuacji. System MES pomógł więc firmie przejść do modelu organizacji samodoskonalącej się. Jednym z rezultatów takiej pracy analitycznej i zespołowej jest znacząca redukcja czasu przezbrojeń.
COVID a MES
system pomaga ograniczyć zbędne przemieszczanie się pracowników w zakładzie
Jeszcze inny przykład pochodzi z Polipack – firmy działającej na polskim rynku od blisko 30 lat, specjalizującej się w produkcji wysokiej jakości opakowań z tworzyw sztucznych dla branży spożywczej, farmaceutycznej, kosmetycznej i tytoniowej. Po wdrożeniu ProSeS BDE system ten stał się w firmie centrum dowodzenia produkcją i parkiem maszynowym, dodatkowo monitorując czas pracy pracowników w dwóch zakładach produkcyjnych. Rozwiązanie dało firmie pełną kontrolę nad procesami produkcji, w tym planowania i harmonogramowania. W rezultacie w zakładach utrzymywane są stale na najwyższych poziomach wskaźniki OEE.
W jaki sposób firma z dobrze skalibrowaną produkcją zareagowała na COVID?
„Zakład produkcyjny do utrzymania ciągłości pracy wymaga fizycznej obecności pracowników. Podobnie jak w innych fabrykach, także i u nas konieczne więc było wdrożenie różnego rodzaju środków bezpieczeństwa. COVID spowodował, że zmuszeni byliśmy szybciej niż to planowano rozpoznać pełne możliwości systemu. Już w czasie pandemii uruchomiliśmy funkcjonalności ProSeS BDE, których wcześniej nie wykorzystywaliśmy. Duża część pracy skupiła się na maksymalnym ograniczeniu mobilności pracowników wewnątrz zakładu. Opracowaliśmy nowe formy raportów i postaraliśmy się, aby z systemu wychodziły jeszcze bardziej rzetelne informacje. Jednym z przykładów zmiany jest obsługa maszyn w czasie przestojów. Do maszyn wzywani są wyłącznie dedykowani specjaliści, którym wcześniej nadaliśmy różne kategorie. Usprawniliśmy też wewnętrzny obieg informacji, tak by każde przemieszczanie się pracownika w hali produkcyjnej było uzasadnione konkretnym zadaniem. Zapewne i tak wdrożylibyśmy tego rodzaju usprawnienia, lecz COVID nam niejako pomógł zrobić to szybciej”
Bartłomiej Więckowski
koordynator ds. Produkcji i IT w Polipack
Użytkownicy zgodnie o korzyściach z rozwiązania MES
Każde z przedsiębiorstw, które wdrożyło system klasy MES, podkreśla, że główną korzyścią z rozwiązania jest uzyskiwanie rzetelnych, wiarygodnych i sprawdzonych informacji. We wszystkich zakładach poprawie uległy najważniejsze wskaźniki określające wydajność, efektywność i jakość produkcji, co bezpośrednio przekłada się na lepsze wyniki finansowe.
W zakładach PipeLife wskaźnik główny OEE udaje się utrzymać na poziomie ponad 80%, pozostały czas zajmują niezbędne konserwacje i przezbrojenia, których czas udało się zredukować do minimum. Przy tak ogromnym portfolio wyrobów (kilka tysięcy pozycji) firma utrzymuje czas przezbrojeń na poziomie poniżej 4%. To przepaść w odniesieniu do stanu, w jakim firma pracowała przed uruchomieniem systemu – wówczas OEE wynosił między 50% a 60%. MES pomaga też nadzorować jakość. W produkcji asortymentu PipeLife jednym z najważniejszych etapów jest zgrzewanie, decyduje ono o trwałości wyrobów. Ponieważ na niektóre produkty firma udziela aż 50 lat gwarancji, zachowanie maksymalnej jakości jest kluczowe, dlatego również w tym wypadku ProSeS BDE sprawdza, czy operatorzy maszyn nie przyspieszają procesu zgrzewania.
Kiedy wydatki na rozwiązanie MES się zwracają?
Do zakupu systemu MES należy podejść jak do inwestycji. „W przypadku zakupu rozwiązania informatycznego trudno jest szacować jego opłacalność. W przypadku maszyny zazwyczaj doskonale wiemy, kiedy się ona zwróci. Z MES jest nieco trudniej, bo jest wiele zmiennych i na początku nie wiadomo, jakie będą efekty. Tak jak wspomniałem, u nas ten rezultat był spektakularny, ponieważ doświadczyliśmy skokowej poprawy OEE aż o 20 procent. Wydatki na rozwiązanie zwróciły się więc bardzo szybko” – mówi Janusz Manteufel.
Z kolei w Polipack, pomimo trwającej pandemii postępują prace nad ciągłym rozwojem systemu i poszerzaniem jego możliwości, który coraz szybciej obejmie kolejne obszary produkcji. „Obecnie wdrażamy nowe moduły ProSeS BDE. COVID, choć wprowadził duże zamieszanie w części popytowej, nie przeszkodził nam w usprawnianiu zakładu. Dzięki dalszej rozbudowie systemu będziemy mieć pełen nadzór nad peryferiami, formami i maszynami, co pozwoli nam lepiej planować i nadzorować przeglądy. Plany serwisowe będą z kolei ściśle zintegrowane z harmonogramowaniem produkcji” – mówi Bartłomiej Więckowski. I dodaje: „dziś nie wyobrażam sobie pracy naszych zakładów bez rozwiązania klasy MES – tej papierologii, przerzucania danych z arkuszy kalkulacyjnych, ciągłych poprawek i braku dostatecznej informacji. Z drugiej strony chcę jednak podkreślić, że aby system rzeczywiście wspomagał firmę, musi za tym stać człowiek. ProSeS BDE nas wspiera, bo został dobrze wdrożony, bo do systemu są wprowadzane dane w sposób właściwy, bo pracownicy i użytkownicy rozumieją, jaki jest sens jego działania”.
odkryj
Historie naszych Klientów: